IoT solution for machine monitoring with vibration sensors
In modern industry, IoT solutions for machine monitoring with vibration sensors are revolutionizing the way companies manage and maintain their equipment. By continuously monitoring and analyzing vibration data in real time, these systems enable precise diagnosis of machine condition and performance. This leads to an optimization of maintenance schedules, a reduction in downtime and an extension of service life. The integration of IoT with vibration sensors provides insight into machine health and offers scaling effects throughout the company with the low-threshold setup of an IoT network.
Avoid machine failure with machine monitoring
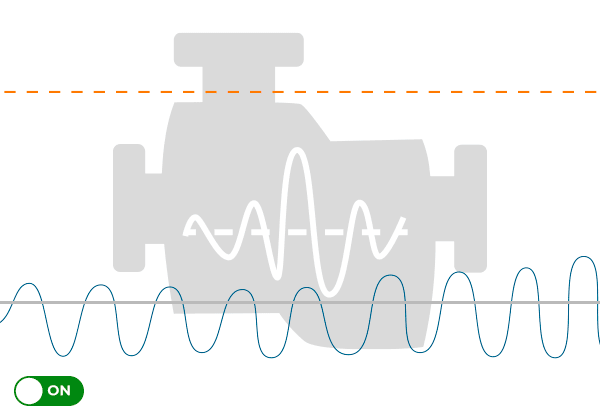
Without machine monitoring with vibration sensor
Early detection of errors
Problems are often not noticed until they have already led to serious damage or breakdowns, resulting in unplanned downtime and expensive repairs
Maintenance planning
Maintenance is often carried out according to a fixed schedule, regardless of the actual condition of the machine, which can lead to unnecessary maintenance work or problems being overlooked.
Productivity and costs
Unplanned downtimes and inefficient machine running times are more frequent, resulting in higher costs due to emergency repairs and production delays.
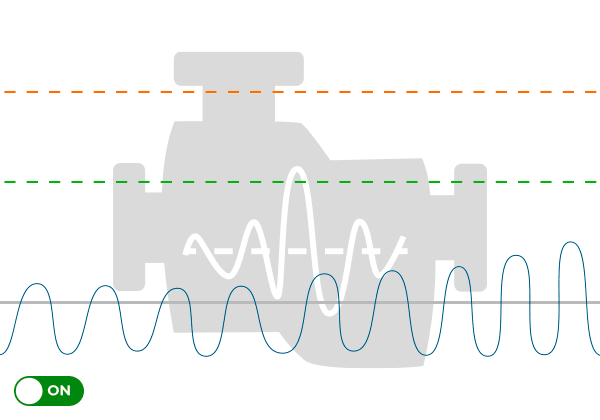
With machine monitoring with vibration sensor
Early detection of errors
Unusual vibrations can be detected at an early stage, indicating incipient problems or failures. This enables proactive maintenance and repair measures to be taken before major damage occurs.
Maintenance planning
Maintenance can be planned based on the actual condition and changes to the machine, resulting in more efficient and cost-effective maintenance cycles. Ideally, maintenance can be carried out at non-production times.
Productivity and costs
By minimizing unplanned downtimes and optimizing machine performance, higher production efficiency and long-term cost savings can be achieved.
Do you want to save valuable time and at the same time utilize the efficiency of IoT in your company?
Our team of experienced IoT consultants is ready to support you. With our comprehensive services and customized solutions, we can help you implement your projects faster and more efficiently. Contact us today and let's discover together the ways we can optimize your processes and help you achieve your goals. Save time and resources - with our expert knowledge at your side.
Functional description based on vibration sensors
When using vibration sensors for machine monitoring, it is crucial that not every sensor measures in the same way or is equally suitable for every situation. The selection of the appropriate vibration sensor depends heavily on the specific requirements of the system to be monitored, the environmental conditions and the objectives of the monitoring. Depending on the situation, other measured values may also be useful or the way in which the vibration patterns were created.
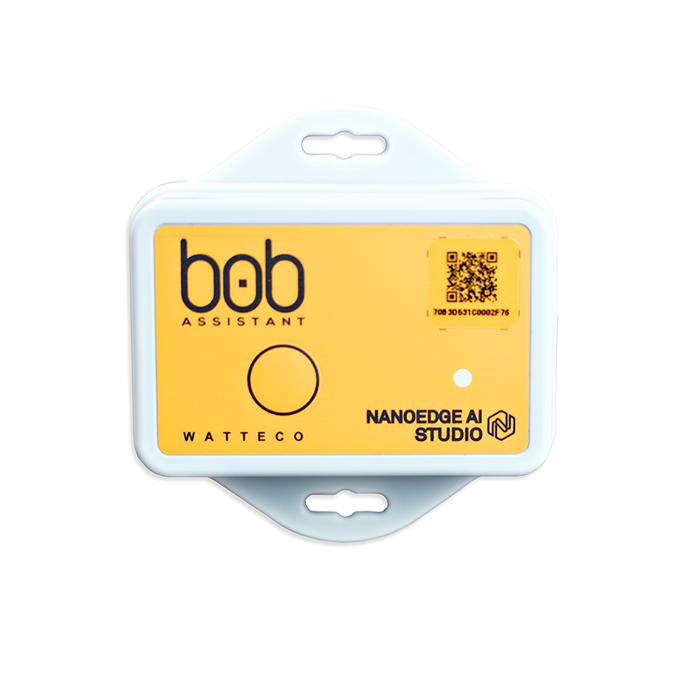
WATTECO BoB Assistant vibration sensor with AI
The BoB Assistant vibration sensor learns the vibrations of the machine on which it has been mounted. There are several ways to do this, including with a screw connection or via the magnet on the back of the sensor. In the first intensive learning phase, the BoB "listens" more closely or more often, then less frequently over the next few days. This phase is completed after 7 days and the sensor assumes that it knows the vibration pattern.
The sensor learns the vibrations of the X-, Y- and Z-axis and measures regularly without sending a LoRaWAN packet. If all measured values are within the learned pattern, it sends a report every 3 hours with the sum of the measured values within this period. In case of an anomaly, the vibration sensor sends a direct alarm.
It is important for the use of this sensor that it is not moved often, as this in turn influences the vibrations. This means that if the sensor or the associated machine has to be moved, the sensor also has to "relearn" the new vibration pattern.
Some machines have several operating modes; the different operating modes can also be learned through machine learning and saved for later recognition.
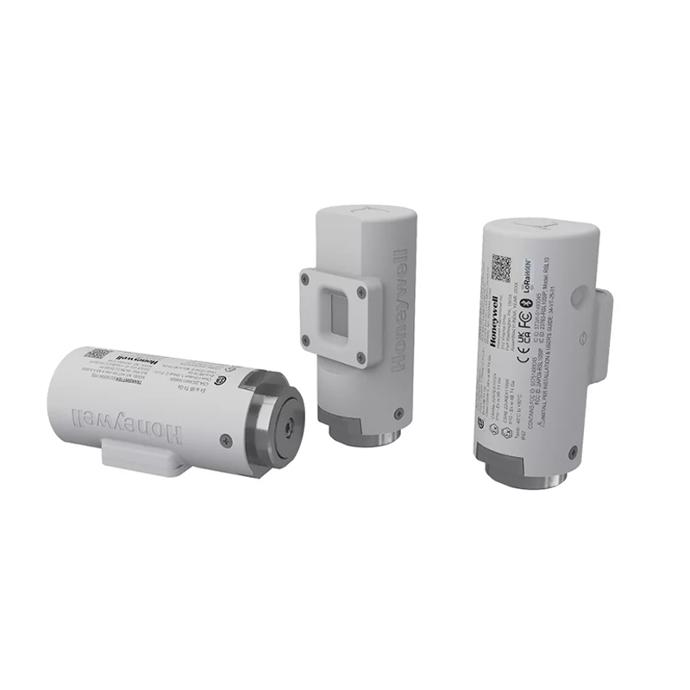
Honeywell HVT100 versatilis EHM transmitter
The vibration sensor HVT100 Versatilis EHM Transmitter evaluates the vibrations of the machine based on the international standard ISO 10816-3. This standard is already integrated in the hardware and does not require any additional software for evaluation or a learning phase. It measures and evaluates machine vibrations in the frequency range from 10 Hz to 1000 Hz.
This standard is particularly relevant for the early detection of possible anomalies in rotating machinery. This can include pumps, ventilation systems and fans as well as electric motors.
However, the vibration sensor from Honeywell does not only rely on vibration measurement of the X, Y and Z axes. In addition to vibrations, measuring the ambient and surface temperature often provides further information about the health of the machine, as does noise. Ambient pressure and humidity can also be used as additional factors for assessment.
The housing of the 6in1 sensor system for machine monitoring has Ex certification. This marking is found on devices and protective systems that are designed for use in potentially explosive atmospheres to prevent the generation of sparks, high temperatures or other ignition sources.
Which vibration sensor is right for me?
Sensors use different ways to reach their destination. Our IoT consultants will be happy to assist you during the decision-making process.